What are the common weaving patterns of composite materials? An Overview When composite applications require multiple fiber orientations, woven fabrics are highly beneficial. This overview presents the fundamentals of woven fabrics and their various types.
In composites manufacturing, where multiple fiber orientations are necessary, fabrics that combine 0-degree and 90-degree fiber orientations are advantageous.
Woven fabrics are created by interlacing warp (0-degree) fibers and weft (90-degree) fibers in a consistent pattern or weave style. The fabric's integrity is preserved through the mechanical interlocking of the fibers. Drape (a fabric's ability to conform to complex surfaces), surface smoothness, and stability are primarily determined by the weave style. Below is a description of some commonly used weave styles:
(A) Plain Weave
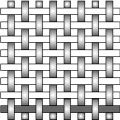 In this symmetrical weave, each warp fiber alternates under and over each weft fiber. It offers good stability and reasonable porosity. However, it has the lowest drape among the weaves, and the high level of fiber crimp results in comparatively lower mechanical properties. Heavy fabrics rarely use this weave style due to excessive crimp with large fibers (high tex).
(B) Twill Weave
One or more warp fibers alternate over and under two or more weft fibers in a regular, repeated manner. This creates a straight or broken diagonal 'rib' appearance in the fabric. Twill weave offers better wet out and drape compared to plain weave, with only a slight reduction in stability. The fabric also has a smoother surface and marginally higher mechanical properties due to reduced crimp.
(C) Satin Weave
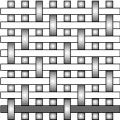 Satin weaves are essentially modified twill weaves with fewer warp and weft intersections. The 'harness' number used in the designation (typically 4, 5, or 8) represents the total number of fibers crossed and passed under before the pattern repeats. A 'crowsfoot' weave is a satin weave variant with a different stagger in the repeat pattern. Satin weaves are very flat, with excellent wet out and drape. The low crimp provides good mechanical properties, allowing fibers to be woven in close proximity, creating fabrics with a tight weave. However, the weave's low stability and asymmetry should be considered. Asymmetry causes one fabric face to have fibers running predominantly in the warp direction, while the other face has fibers running predominantly in the weft direction. Care must be taken when assembling multiple layers of these fabrics to prevent stress buildup due to this asymmetric effect.
(D) Basket Weave
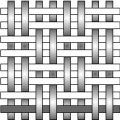 Similar to plain weave, basket weave involves two or more warp fibers alternately interlacing with two or more weft fibers. A 2x2 basket arrangement has two warps crossing two wefts, but the fiber arrangement doesn't have to be symmetrical (e.g., 8x2, 5x4). Basket weave is flatter and stronger than plain weave due to less crimp but is less stable. It is used for heavyweight fabrics made with thick (high tex) fibers to avoid excessive crimping.
(E) Leno Weave
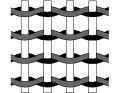 Leno weave enhances stability in 'open' fabrics with a low fiber count. In this plain weave variation, adjacent warp fibers twist around consecutive weft fibers, forming a spiral pair and effectively 'locking' each weft in place. Leno weave fabrics are typically used alongside other weave styles, as their openness alone is insufficient for producing effective composite components.
(F) Mock Leno Weave
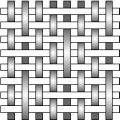 This plain weave variant features occasional warp fibers that deviate from the alternate under-over interlacing and instead interlace with every two or more fibers at regular intervals, usually several fibers apart. This occurs similarly in the weft direction, resulting in a fabric with increased thickness, a rougher surface, and additional porosity.
(G) Woven Glass Yarn Fabrics vs. Woven Rovings Yarn-based fabrics generally provide higher strengths per unit weight than roving and, being finer, produce fabrics on the lighter end of the available weight range. Woven rovings are less expensive to manufacture and offer better wet out. However, as they are only available in heavier texes, they can only produce fabrics on the medium to heavy end of the available weight range. Consequently, they are more suitable for thick, heavier laminates.
In conclusion, understanding the different weave styles of composite woven fabrics is crucial for selecting the appropriate fabric for your specific application. Each weave style offers its unique characteristics, advantages, and limitations, allowing you to choose the ideal fabric for your composite needs. By familiarizing yourself with the various types of woven fabrics, you will be better equipped to make informed decisions that contribute to the success and growth of your composite projects.
|