(1) Over 20 year production experiences in carbon pultruded profiles production.
Galaxys has been producing carbon fiber and fiberglass pultruded profiles for 20 years, with stable production technology and product quality. Our product specifications are complete, and the prices are very competitive. Our pultruded profiles use continuous unidirectional carbon fiber or glass fiber, and vinyl ester resin as the main raw materials. If required by customers, epoxy resin can also be used.
(2) Pultrusion introduction
Pultrusion is a process where continuous unidirectional fibers are impregnated in a resin bath, mixed with resin, and then heated and formed through a pultrusion die. This gives the product excellent tensile strength along the fiber arrangement direction. Theoretically, the length of the pultruded profile can be infinitely extended if the fiber strands are not interrupted. Our thinnest pultruded profile has a diameter of 0.5mm.
(3) Production process
(a)Fiber impregnation
Continuous unidirectional carbon fiber or glass fiber is fed into a resin bath for impregnation, allowing the fiber to fully absorb the resin.
(b)High-temperature pultrusion molding
The impregnated fiber and resin are heated and formed through a pultrusion die.
(c)Cooling and setting
The molded product undergoes a cooling process to maintain its shape and performance. d. Cutting and shaping: The cooled profile is cut to the required length.
(4)Advantages of GLX Pultruded Profiles
(a)High tensile strength
The product has good tensile strength along the fiber arrangement direction.
(b)Lightweight
Carbon fiber pultruded profiles are lightweight, making them easy to transport and install.
(c)High rigidity
Carbon fiber pultruded profiles have better rigidity than fiberglass pultruded profiles.
(d)High customization
Different shapes and sizes of profiles can be produced according to customer needs.
(e)Chemical properties
Vinyl ester pultruded profiles have good corrosion resistance and fatigue resistance, as well as higher heat resistance and chemical stability.
(5)Disadvantages
(a)Weak circumferential compressive strength
Due to the lack of a 90-degree circumferential fiber structure, pultruded profiles have weaker circumferential compressive strength compared to rolled tubes and filament-wound tubes.
(b)Slower production speed with epoxy resin
If the customer chooses epoxy resin, the production process is slower and less efficient.
With twenty years of industry experience and mature, stable pultrusion production technology, our company provides high-quality carbon fiber and fiberglass pultruded profiles for customers. Our products are widely used in fields such as model aircraft, kites, tents, antenna poles, fishing rods, sports equipment, and more. We are always committed to meeting customer needs and providing excellent products and services.
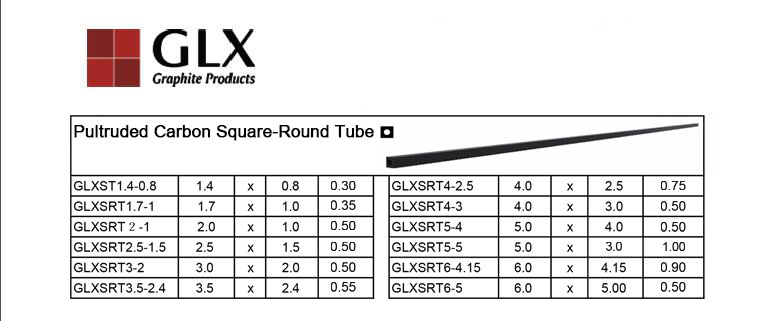
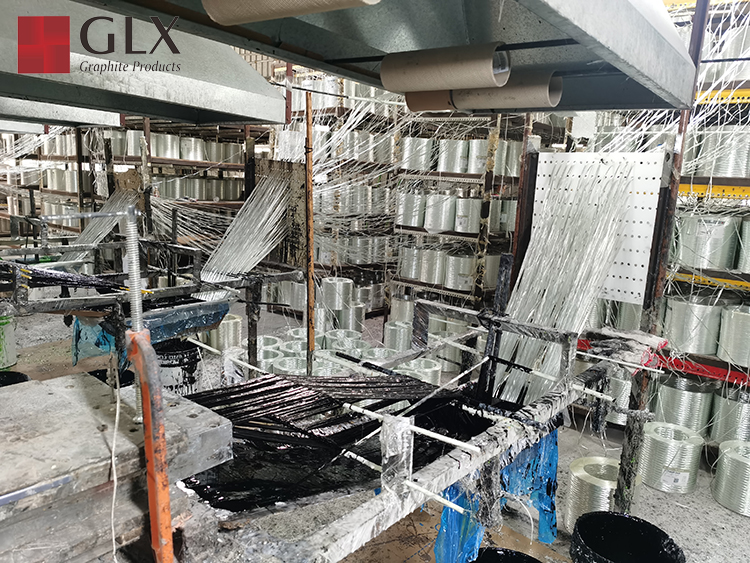
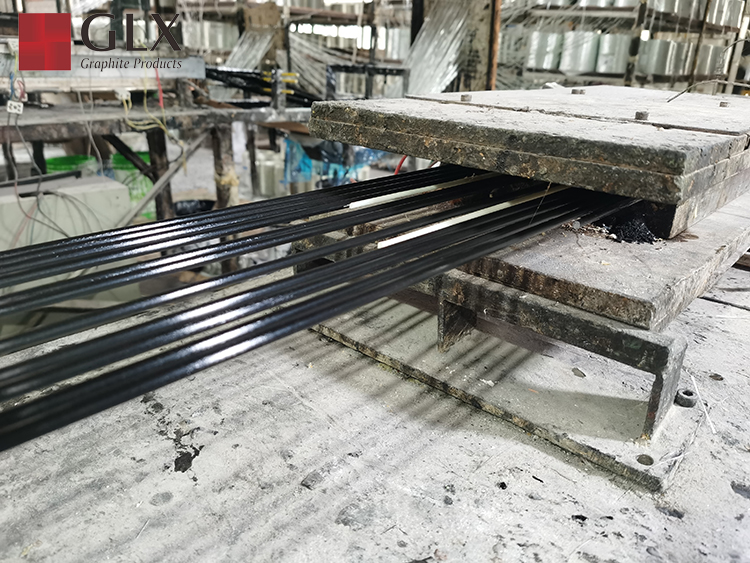
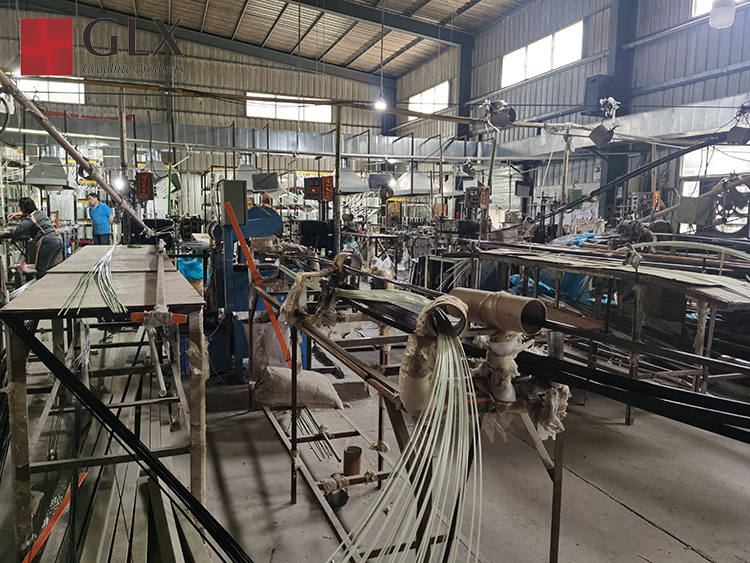
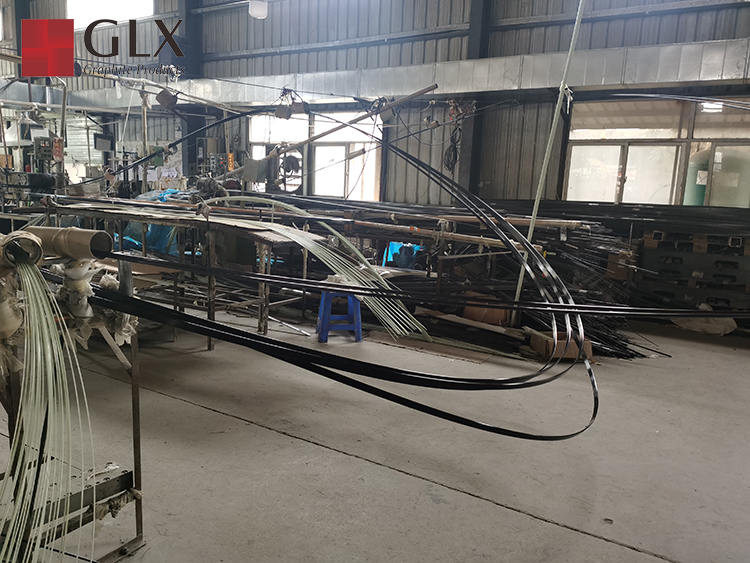
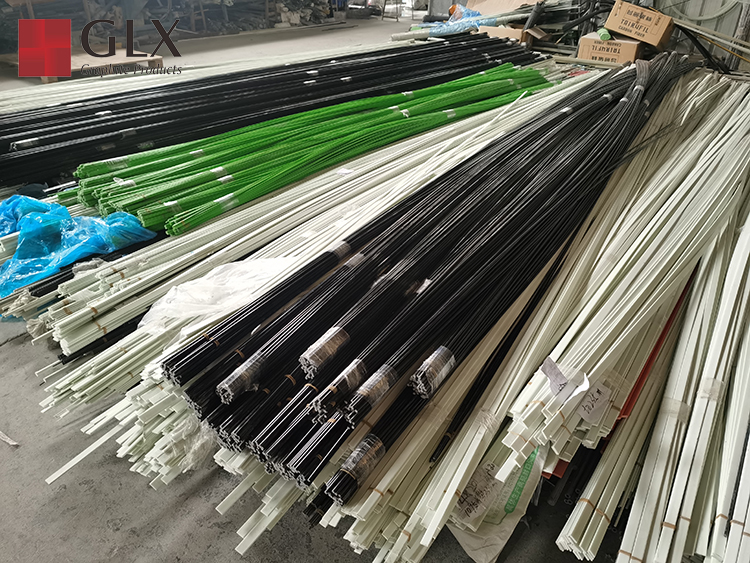
我们生产碳纤维和玻璃纤维拉挤型材已经20年,生产技术和产品质量都很稳定。我们的产品规格齐全,价格也很有竞争优势。我们的拉挤型材以连续性的单向碳纤维或玻璃纤维。以及乙烯基树脂为主要原料。如客户要求,也可选用环氧树脂。
(1)拉挤成型简介
拉挤成型是将连续性的单向纤维经过树脂槽进行浸渍,与让纤维与树脂混合后,再通过拉挤模具进行高温加热成型。这使得产品沿纤维排列方向具有优异的抗拉伸强度。如果纤维丝不中断,拉挤型材的长度理论上可以无限延长的。我们最细的拉挤型材直径是0.5mm。
(2)生产流程
a. 纤维浸渍:将连续性的单向碳纤维或玻璃纤维送入树脂槽进行浸渍,使纤维充分吸附树脂。
b. 高温拉挤成型:将浸渍好的纤维和树脂通过拉挤模具进行高温加热成型。
C. 冷却定型:成型后的产品经过冷却过程以保持其形状和性能。
D. 切割成型:将冷却定型后的型材切割成所需的长度。
(3)优点:
1.高拉伸强度:产品沿纤维排列方向具有良好的抗拉伸强度。
2.轻质:碳纤维拉挤型材重量轻,便于运输和安装。
3.高刚性:碳纤维拉挤型材刚性优于玻璃纤维拉挤型材。
4.定制性强:可根据客户需求生产不同形状和尺寸的型材。
5.化学性能:乙烯基拉挤型材有良好的耐腐蚀性和耐疲劳性,也有更高的耐热性和化学稳定性。
(4)缺点:
1. 环向抗压能力较弱:由于没有90度的环向纤维结构,拉挤型材相比卷管和缠绕管材在环向抗压能力方面较弱。
2. 使用环氧树脂生产速度较慢:如果客户选择环氧树脂,生产过程速度较慢,效率较低。
凭借二十年的行业经验和成熟稳定的拉挤生产技术,我们公司为客户提供优质的碳纤维和玻璃纤维拉挤型材。我们的产品广泛应用于航模、风筝、帐篷、天线杆、钓鱼竿、运动器材等领域。我们始终致力于满足客户需求,提供优质的产品和服务。
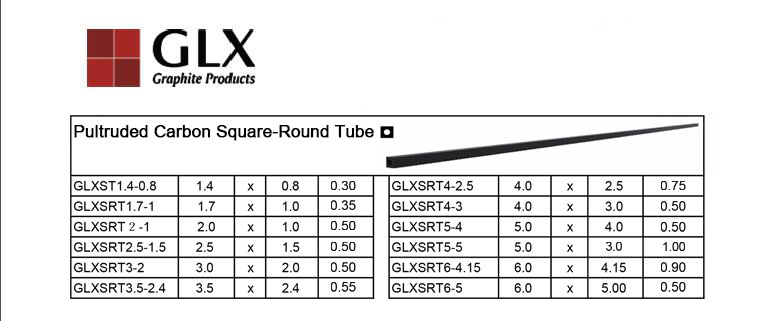
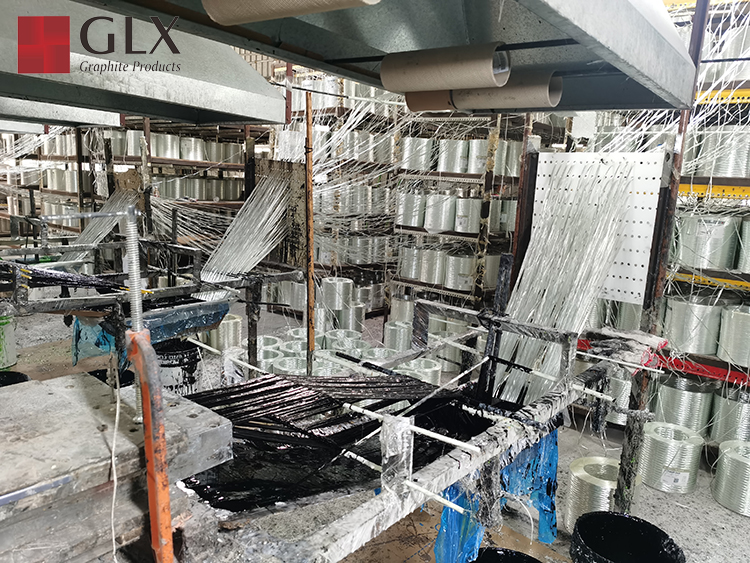
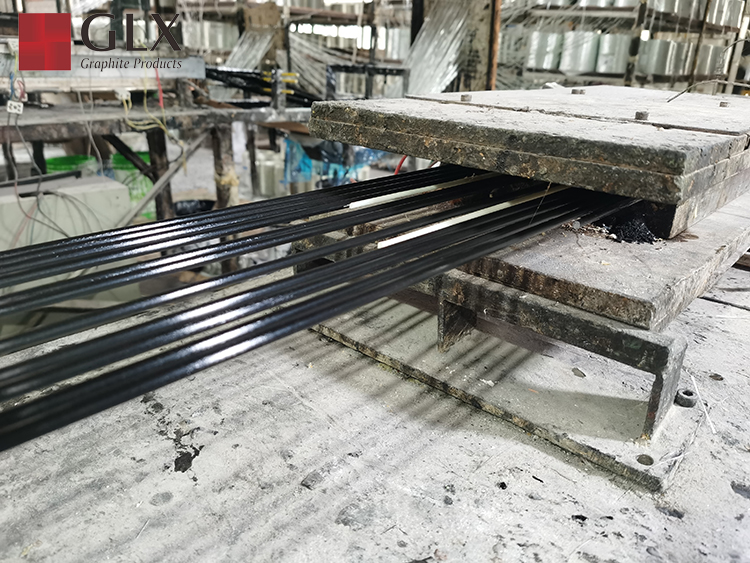
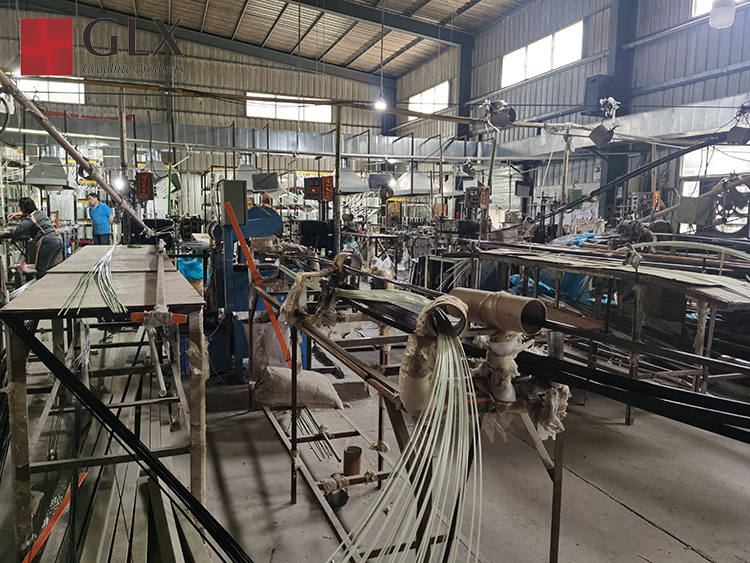
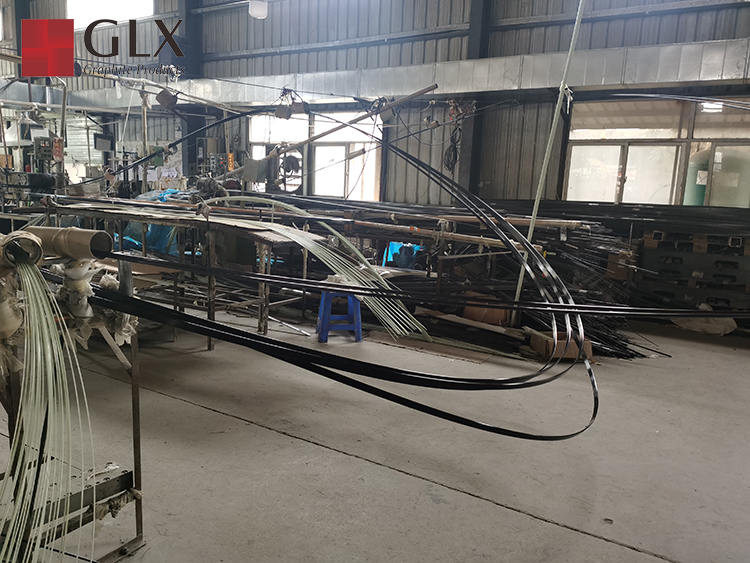
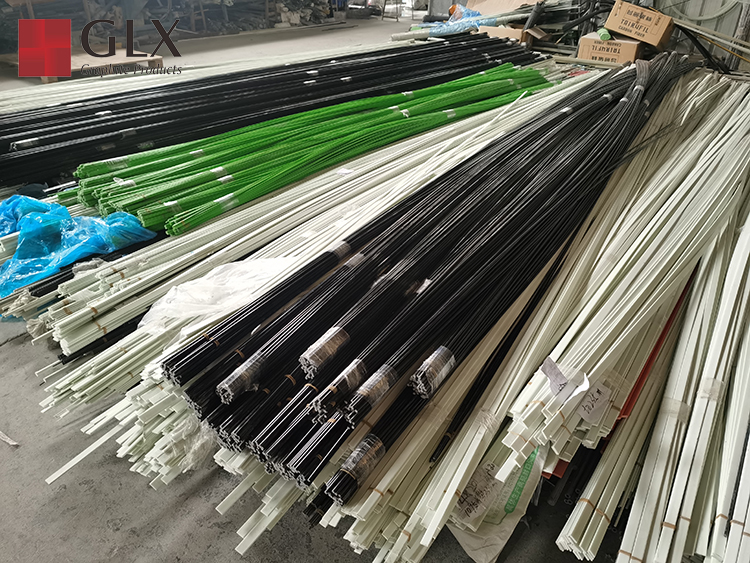